دانلود با لینک مستقیم و پر سرعت .
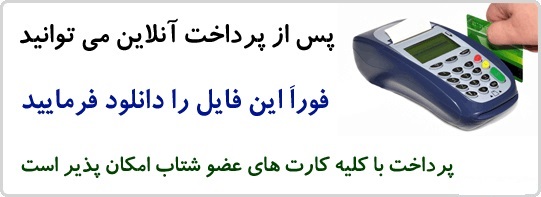
لینک دانلود و خرید پایین توضیحات
فرمت فایل word و قابل ویرایش و پرینت
تعداد صفحات: 10
عوامل خوردگی کوره دیگ بخار:
یکی از مشکلات اساسی که می تواند باعث بروز مشکل برای کوره ها باشد، خوردگی در نقاط و وسایل مختلف آن است که ضمن هدر رفتن
مقدار زیادی انرژی، آسیب های مکانیکی متعددی به کوره وارد می
کند. از آنجا که هر کوره از بخش های متعددی همچون بدنه، اطاقک
احتراق (Fire Chamber)، دودکش، مشعل و سایر تجهیزات جانبی تشکیل
شده، لذا علل خوردگی و راه حل های پیشنهادی در هر یک از بخش ها
به طور مجزا مورد بحث و بررسی قرار می گیرد.
بدنه کوره :
معمولاً بدنه یا دیواره خارجی کوره ها را از ورقه استیل16/3 و کف
آن را از ورقه 4/1 می سازند.
در طراحی ها عموماً اتلاف حرارتی از بدنه کوره حدود 2 درصد منظور
می شود. نوع و ضخامت عایق کاری بدنه داخلی کوره باید طوری در نظر
گرفته شود که دمای سطح خارجی کوره بیش از (1800° F) نشود. اصولاً
عایق کاری و عایق های به کار رفته در کوره ها از نظر سرویس دهی
مناسب، عمر معینی دارند و به مرور زمان ساختمان کریستالی آنها
تغییر یافته و ضخامت آنها کم می شود و این تغییرات ساختمانی سبب
تغییر ضریب انتقال حرارت و اتلاف انرژی به بیرون خواهد بود.
مطالعات میکروسکپیک و کریستالوگرافیک چند نمونه عایق کار کرده،
با نوع تازه آن موید این مطلب است. در صورتی که عایق دیواره های
کوره بر اثر بنایی ناصحیح، عدم انجام صحیح Curing بر مبنای
دستورالعمل، حرارت زیاد و یا شوک های حرارتی ترک بردارد، نشت
گازهای حاصل از احتراق که عبارتند از: So x، No x، N2،Co2
(درصورتی که نفت کوره به عنوان سوخت مصرف شود) و بخار آب در
لابلای این ترک ها و تجمع آنها در لایه بین بدنه کوره و عایق
دیواره و سرد شدن تدریجی آنها تا دمای نقطه شبنم، باعث خوردگی
بدنه می شود.
تداوم این امر ضمن اتلاف مقدار بسیار زیاد انرژی (از طریق بدنه
کوره به محیط اطراف)، باعث ریختن عایق و در نتیجه اتلاف بیشتر
انرژی و گسترش خوردگی بر روی بدنه کوره و سایر نقاط آن خواهد شد.
در یک بررسی ساده بر روی کوره ای که چندین سال از عمر عایق آن می
گذشت ملاحظه شد که دمای اندازه گیری شده واقعی سطح کوره در اکثر
نقاط بسیار بیشتر از میزان طراحی است. این مقدار در بعضی از
موارد به (1800° F) نیز می رسید.
در این کوره ضمن جدا شدن عایق از دیواره کوره و گسترش خوردگی در
نقاط مختلف بدنه، گرم شدن بدنه کوره نیز موجب خم شدن دیواره ها
شده و سرعت خوردگی را افزایش داده و باعث خرابی قسمت های مختلف
کوره شده است. به طور کلی برای جلوگیری و یا کاهش مشکلات خورندگی
بر روی بدنه کوره لازم است به هنگام تعمیرات اساسی ضمن توجه به
عمر عایق دیواره در صورتی که عمر آنها از حد معمول گذشته باشد
(البته با توجه به درجه حرارتی که درهنگام کار کردن واحد درمعرض
آن بوده اند) آنها را با عایق مناسب و استاندارد تعویض کرد و در
صورت وجود ترک (قبل و یا بعد از بنایی)، محل ترک ها را با الیاف
مخصوص KAOWOOL پر کرد. همچنین در بنایی، عملیات Curing را مطابق
دستور العمل انجام داد تا پیوند هیدرولیکی در عایق های بکار رفته
در بنایی، به پیوند سرامیکی تبدیل شده و میزان رطوبت باقیمانده
در دیواره از 0.4 gr/m2 بیشتر نشود.
البته چنانچه Ceramic Fiber (الیاف سرامیکی) به عنوان عایق
دیواره کوره مورد استفاده قرار گیرد، بدلیل عدم نیاز به Curing و
Drying و سبکی وزن، مشکلات احتمالی استفاده از عایق های نیازمند
به Curing را نخواهیم داشت. ضمن این که عمر بیشتر و چسبندگی
بهتری به دیواره، نسبت به دیگر عایق های موجود دارند.
تیوب ها یا لوله های داخل کوره:
معمولاً کوره ها متشکل از دو بخش RADIATION و CONVECTION هستند
که بایستی ظرفیت گرمایی (DUTY) کوره از نظر درصد، تقریباً به
نسبت70 و30 درصد بین این دو بخش تقسیم شود.
از آنجا که لازم است سیال به اندازه دمای مورد نظرگرم شود بایستی
حرارت مورد نیاز خود را از طریق هدایتی از لوله ها و تیوب های
داخل کوره دریافت کند، این لوله ها نیز حرارت مورد نیاز برای این
انتقال حرارت را از طریق تشعشعی و جابجایی در اثر احتراق سوخت در
داخل کوره جذب می کنند. انتخاب آلیاژ مناسب جهت لوله با توجه به
نوع سیال و ترکیبات آن و میزان حرارت دریافتی توسط لوله و در
معرض شعله قرار گرفتن از اهمیت بسزایی برخوردار است.
مسائلی که به بروز مشکلاتی برای تیوب ها منجر می شود عبارتند از:
سرد و گرم شدن ناگهانی لوله، گرم شدن بیش از حد لوله و بالا رفتن
دمای تیوب از حداکثر مجاز آن، در معرض شعله قرار گرفتن و برخورد
شعله به لوله (impingement) ، ایجاد یک لایه کُک بر روی جداره
داخلی لوله، Carborization، Hogging، Bending، Bowing، Sagging،
Creeping، خوردگی جداره داخلی لوله بر اثر وجود مواد خورنده در
سیال عبوری، خوردگی جداره بیرونی لوله در اثر رسوبات حاصل از
احتراق سوخت مایع بر روی جداره خارجی لوله، کارکرد لوله بیش از
عمر نامی آن (80 هزار الی 110 هزار ساعت)
سرد و گرم شدن ناگهانی لوله، ممکن است به Creeping (خزش) که
نتیجه آن ازدیاد قطر لوله می باشد منجر شود که در این صورت
احتمال پارگی لوله و شکنندگی آن را افزایش می دهد. چنانچه در اثر
Creeping مقدار ازدیاد قطر از 2 درصد قطرخارجی لوله بیشتر شود،
لوله مزبور بایستی تعویض شود.
در یک اندازه گیری عملی که برای برخی از تیوب های هشت اینچی و شش
اینچی کوره (کوره تقطیر در خلا) H-151 در هنگام تعمیرات اساسی
صورت پذیرفت، محاسبات زیر بدست آمد:
برای تیوب "8
OD = 8.625 (اصلی)
OD = 8.75 (اندازه گیری شده)
(OD = (0.125 (افزایش قطر لوله)
(OD ALLOWABLE = (8.625x2%=0.1725
هنوز می توان از تیوب مزبور استفاده کرد.
برای تیوب "6
OD = 8.625 (اصلی)
OD = 8.675 (اندازه گیری شده)
(OD = (0.05 (افزایش قطر لوله)
(OD ALLOWABLE = (6.625x2%=0.1325
که هنوز می توان از تیوب شش اینچی مزبور استفاده کرد.
همان طور که مشخص است تیوب 8 حدوداً بیش از دو برابر تیوب 6
ازدیاد قطر داشته است.
برای لوله "6
کوره H-101 (اتمسفریک)
OD =6.625 (اصلی)
OD = 6.635 (اندازه گیری شده)
OD =0.01 (اندازه قطر لوله)
(OD ALLOWABLE = (6.625x2%=0.1325
بالا نگه داشتن دمای پوسته تیوب ها سبب کاهش مقاومت لوله ها و
کاهش عمر مفید و گارانتی حدود یکصد هزار ساعتی آنها می شود.
تجربه نشان داده است که اگر به مدت 6 هفته سطح خارجی (پوسته)
لوله ای 900°C بیش از مقدار طراحی در معرض حرارت قرار بگیرد، عمر
تیوب ها نصف می شود.
یکی دیگر از مشکلات پیش آمده برای لوله ها، برخورد شعله به لوله
(IMPINGEMENT) است، که باعث OVER HEATING کوره و در نهایت HOT
SPOT می شود. این امر می تواند ضمن لطمه زدن در محل برخورد شعله
به لوله، باعث تشدید عمل کراکینگ مواد داخل لوله شود و مواد
مزبور به دو قسمت سبک و سنگین تبدیل گردند.
مواد سنگین به جداره داخلی لوله چسبیده و کک ایجاد می کنند. به
ازای تشکیل یک میلی لیتر ضخامت کک با توجه به ضریب هدایتی کک که
برابر مقدار خاصی می باشد برای یک شارژ حرارتی معمول در قسمت
تشعشعی کوره H-101 (اتمسفریک) می باشد، معادل فرمول زیر است:
می بایستی 300°C دمای پوسته تیوب بالاتر رود تا سیال موجود در
تیوب به همان دمای موردنظر برسد. در این صورت ملاحظه می شود بالا
رفتن دمای تیوب به چه میزان اتلاف سوخت و انرژی، داشته و به طور
کلی به مرور زمان چه لطمه ها و آسیب هایی به کل کوره وارد می
شود. به عبارت دیگراختلاف دمای پوسته تیوب های کوره که در طراحی
عموماً 1000°F بالاتر از دمای متوسط سیال درون آن در نظر گرفته
می شود، به مرور زمان با تشکیل کک (با رسوبات بیرونی) بیشتر می
شود.
مشکل دیگر که به علت دمای بالا برای تیوب های کوره ها ایجاد می
شود خمیدگی در جهت های مختلف این تیوب هاست.
یکی دیگر از مسائلی که باعث خم شدن و شکستگی لوله ها می شود
پدیده کربوریزیشن (carborization) است که بر اثر ترکیب کربن با
آهن پدید می آید: این واکنش که باعث تولید کربور آهن خواهد شد در
دمای بالاتر از 7000°c ایجاد می شود 7000°C)تا 14000°C). این
حالت عمدتاً در زمان Curing و drying کوره پدید می آید. البته
Hot spot نیز بیشتر در این زمان ها اتفاق می افتد.
وجود ناخالصی های مختلف مثل فلزات سدیم، وانادیم، نیکل و غیر...،
فلزاتی مثل گوگرد و ازت به صورت ترکیبات آلی در سوخت های مایع،
مسائل عدیده ای را باعث می شوند، که از آن جمله کاهش انتقال
حرارت از طریق سطح خارجی تیوب به سیال درون تیوب است که به علت
تشکیل رسوبات مربوط به ناخالصی های مزبور بخصوص رسوبات فلزی بر
روی تیوب هاست. به همین دلیل برای رسیدن به دمای مورد نظر سیال
موجود در لوله، مجبور به مصرف سوخت بیشتر خواهیم شد. در نتیجه
مشکلات ایجاد گرمای بیشتر در کوره و مسائل زیست محیطی در اثر
تشکیل SOX، NOX و ... را خواهیم داشت. از طرفی به دلیل نشست این
رسوب ها بر روی تیوب ها مسئله خوردگی و سوراخ شدن پیش خواهد آمد.
علت این خوردگی که از نوعHigh temp corrosion می باشد پدیده
سولفیدیش است، که در دماهای بین630°C تا700°C بوقوع می پیوندد.
همان طور که گفته شد علت اصلی آن وجود عناصر وانادیم، گوگرد،
سدیم و نیکل به همراه گازهای حاصل از احتراق سوخت است.
فلزات ذکر شده (بصورت اکسید) به کمک این گازها بالا رفته و بر
روی تیوب های قسمت تشعشع و جابه جایی می نشینند. خوردگی و سوراخ
شدن تیوب، بر اصل اکسید شدن و ترکیب عناصر مزبور باآلیاژ تیوب
استوار بوده که باعث ایجاد ترکیبات کمپلکس با نقطه ذوب پایین می
شود.
ترکیب اولیه پس از Na2SO4، سدیم وانادایت به فرمول Na2O6V2O5 است
که نقطه ذوب آن 6300°C می باشد. عمده ترکیبات دیگر که شامل
کمپلکسی از ترکیب پنتا اکسید وانادیم و سدیم است در شرایطی به
مراتب ملایم تر و درجه حرارتی پایین تر ذوب می شوند. برای مثال
مخلوط وانادیل وانادیت سدیم به فرمول Na2OV2O411V2O5 و
متاوانادات سدیم به فرمول Na2OV2O5 در 5270°C ذوب می شوند. ذوب
این کمپلکس ها شرایط مساعدی را برای تسریع خوردگی بوجود می آورد.
در اینجا ترکیبات حاصل از احتراق نه تنها به نوع ناخالصی بلکه به
نسبت آنها نیز بستگی کامل دارد و در مورد وانادیم میزان سدیم از
اهمیت خاصی برخوردار است.
البته سدیم وانادیل وانادایت پس از تولید و ذوب شدن، با فلز
آلیاژ مربوط به تیوب، ترکیب شده و بر اثر سیال بودن از سطح آلیاژ
کنار رفته و سطوح زیرین تیوب مربوطه در معرض ترکیب جدید قرار می
گیرد. ادامه این وضع به کاهش ضخامت تیوب و در نهایت سوراخ شدن و
از کار افتادن آن منجر می شود.
مشعل ها و سوخت:
نقش کیفیت نوع سوخت و نوع مشعل ها شاید از همه عوامل یاد شده در
کارکرد مناسب، راندمان بیشتر و کاهش خوردگی بیشتر برخوردار باشد.
چنانچه از مشعل های Low excess air و یا نوع مرحله سوز (stage
burning) استفاده شود، هوای اضافی مورد نیاز به میزان قابل توجهی
کاهش یافته و به حدود 3 و 5 درصد می رسد که ضمن کاهش و به حداقل
رساندن گازهای خورنده و مضر زیست محیطی مثل NOx، Sox، در بالا
بردن راندمان کوره بسیار موثر خواهد بود. این امر باعث کاهش مصرف
سوخت شده، و در نتیجه باعث کاهش گازهای حاصل از احتراق و آسیب
رساندن به تیوب ها، بدنه کوره و دود کش ها خواهد شد. وضعیت
عملکرد مشعل ها بایستی به طور مداوم زیر نظر باشد. بد سوزی مشعل
ها می تواند دلایل متضادی، همچون نامناسب بودن سوخت، عیب
مکانیکی، کک گرفتگی سرمشعل و یا بالعکس، رفتگی و سائیدگی
(Errosion) بیش از حد سر مشعل، کمبود بخار پودر کننده و ...
داشته باشد. وجود مواد آسفالتی، افزایش مقدار کربن باقیمانده
(carbon residue) ، بالا بودنِ مقادیر فلزات مثل سدیم، نیکل،
وانادیم و هم چنین سولفور در سوخت مسائل متعددی را در سیستم
احتراق ایجاد می کند که این مسائل به طور کلی به دو دسته تقسیم
می شوند.
الف - مسائل عملیاتی قبل از مشعل ها و احتراق:
این مسایل در اثر وجود آب و نمک ها و ته نشین شدن آنها در ذخیره
سازی نفت کوره بوجود می آیند. در این رابطه عدم تخلیه مداوم مخزن
ذخیره سازی، خوردگی و مشکلات ایجاد شده به طور خلاصه عبارتست از:
تشکیل لجن (sludge) در مخزن در اثر عدم استخراج کامل نفت کوره و
آب، انباشته شدن لجن در فیلترها در اثر محصولات ناشی از خوردگی و
پلیمریزاسیون هیدروکربورهای سنگین به علت اثر کاتالیزوری محصولات
ناشی از خوردگی، انباشته شدن لجن و صمغ های آلی در گرم کننده
سوخت، گرفتگی و خوردگی در نازل های پودر کننده نفت کوره